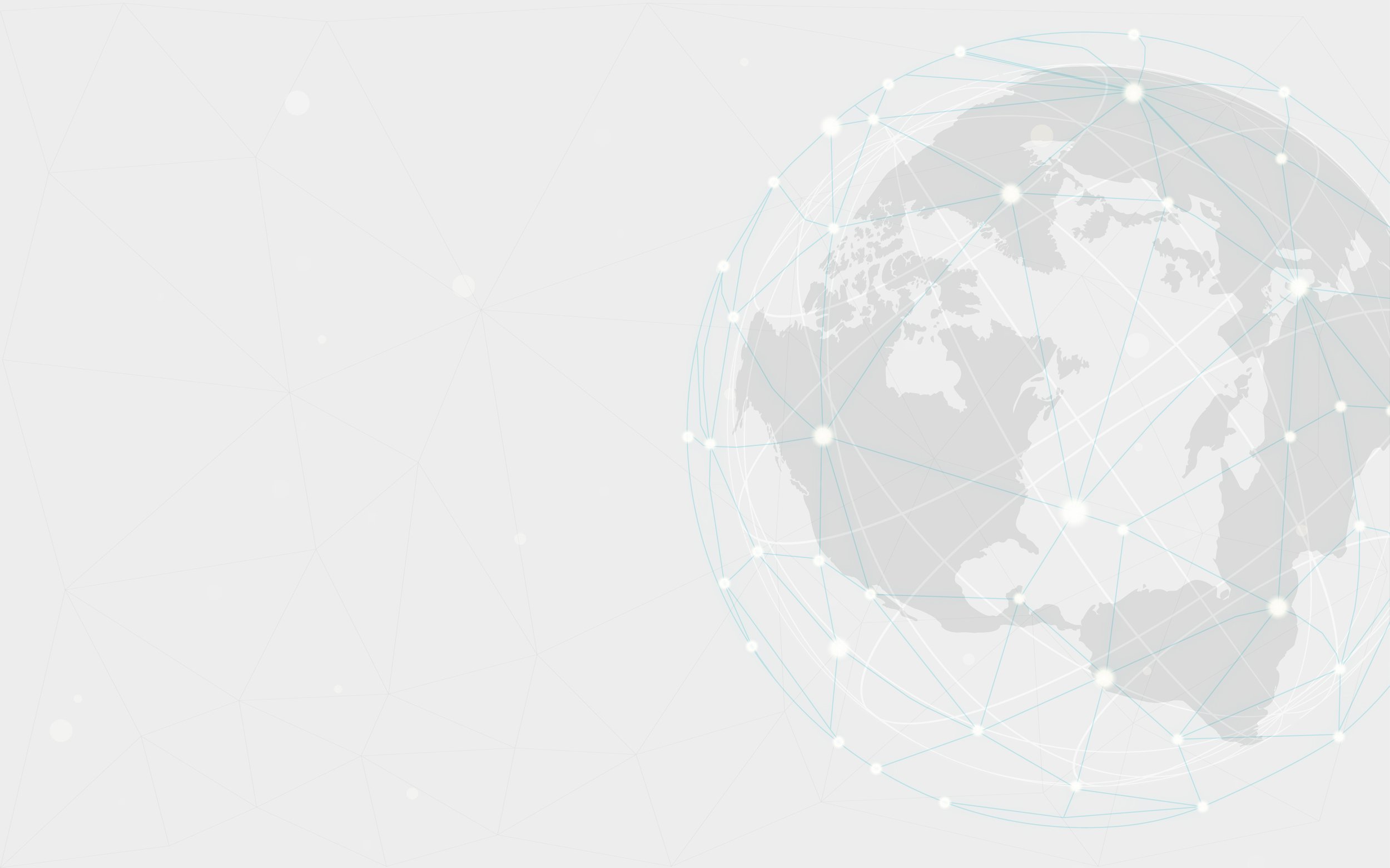
Projects
Thermal Engineering in Automotive Lighting
Automotive lighting faces thermal challenges due to compact designs and high-power LED sources, risking overheating and reduced lifespan. CFD simulations are vital, allowing precise analysis of airflow and heat transfer, ensuring optimal cooling strategies. Utilizing CFD ensures efficient thermal management, enhancing reliability and longevity of automotive lighting systems.
Simulation conditions:
Total thermal power: ~50W
Type of cooling: Natural convection
Operating ambient temperature: 50C
Max LED junction temperature: 125C
Key takeaways :
Material optimization based on max temperature prediction - saves weight and cost
Using passive cooling techniques (when possible) helps reduce overall cost
Heat sink optimization through iterative process can reduce weight and offer more cost-save options
Electronic Systems Cooling
PCB board development faces thermal challenges due to increasing component density and power consumption, leading to hotspots and reliability issues. Incorporating PCB-level details in thermal analysis allows for precise simulation of heat flow, aiding in the identification of potential hotspots and the design of effective cooling solutions to mitigate thermal concerns. This approach helps design the best thermal heat strategy, hence reducing the size of the package envelope.
Simulation conditions:
Total thermal power: ~35W
Type of cooling: Natural convection
Operating ambient temperature: 85C
Max junction temperature: 125C
Key takeaways:
Using PCB level information (ODB++/IDF file, PDML files etc) provides accurate representation of heat transfer path, hence providing accurate results
Gives insight on planning thermal strategy for the module starting at board level - saves cost
Through simulation, other thermal sinking strategies can be validated (heatsinks, heat pipes, TIM etc) thus providing a cost and performance centric solution
Thermal Engineering in ADAS Camera
ADAS cameras face thermal challenges due to compact designs and high-performance requirements, risking overheating and degraded performance. By simulating various design configurations, CFD helps engineers optimize ventilation systems, placement of heat sinks, material selection and simulating heat transfer within camera housings, helping the development of efficient cooling solutions to ensure optimal functionality and prevent overheating.
Simulation conditions:
Total thermal power: ~40W
Type of cooling: Natural convection
Operating ambient temperature: 80C
Max junction temperature: 125C
Key takeaways :
Simulating the module in different boundary conditions helps determine camera thermal performance. Reduces testing & prototyping costs
Provides insight into other cost save options - anodization requirement, type of Thermal Interface Material (TIM) etc
Simulation also helps determine the thermal conductivity of the materials required and how it can help offset cost of using higher cost cooling solutions
Thermal Management of EV Battery
EV batteries encounter thermal challenges due to high energy density, leading to overheating and performance degradation. Effective thermal management involves precise monitoring and regulation of battery temperature through cooling systems, ensuring optimal operation, safety, and longevity of the battery pack under varying conditions, thereby enhancing overall vehicle performance and reliability.
Simulation conditions:
Total thermal power: ~72W / cell (3C)
Type of cooling: Liquid cooling
Operating ambient temperature: 35C
Average cell temperature: 52C
Key takeaways:
Simulation helps identify the temperature distribution and variation between cells in the pack
Different C-rates can be easily simulated and maximum temperatures can be determined
Through simulation cooling channels can be optimized to save cost